spirax sarco pressure relief valve
pressure relief valve vs safety relief valve
butterfly vs ball valve
swing check valve symbol
With the upgrade of automation, the application of solenoid valve pressure control valves in control valves is becoming more and more common, we can see not only butterfly type control valves, ball type control valves equipped with solenoid valves, but many globe type control valves also installed solenoid valves. For the improvement of process requirements, we need to understand the function and role of the solenoid controlled valve once again.

What is SOV(Solenoid Operated Valve)
Solenoid valves are often used in applications where a control valve is required to be actuated quickly to a fault position under certain conditions. It is generally designed to be in the air supply line and is an important accessory to the air control system. The signal from the solenoid coil valve controls the action of the internal valve assembly, allowing flow through the valve in one position and isolating or venting air in the other.
Why is a Single SOV required on a Control Valve?
For example in the case, if a control valve has to be quickly opened in an emergency, a two-way SOV is fitted between the output port of the positioner and the inlet port of the actuator.
How Does A Solenoid Valve Work
When the SOV is activated, the inlet port of the solenoid valve is linked to the outlet, enabling air to flow from the positioner output to the actuator.
The output of the SOV is connected to the exhaust port when it is de-energized, quickly venting air into the control valve to move it to the fail-safe position.
Why Dual SOV on a Control Valve Is Required?
Due to a single solenoid valve for the control valve process, in special failures, such as solenoid valve coil open circuit, blown fuse, plunger stuck, etc. lead to the failure of a single solenoid valve, which eventually leads to some unnecessary process disruption and significant losses due to the plant’s inability to normally closed solenoid valve close/open the control valve at the important position.
So for the purpose of redundancy, the dual solenoid valve design process is used on special and important occasions.
Dual Solenoid Valve Circuits
In the figure below, a dual SOV pneumatic schematic is shown.
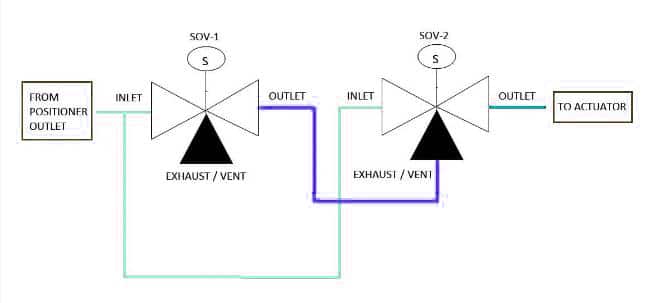
Consider that the actuator receives air constantly under typical circumstances.
The positioner output is linked to both SOV inlets, the SOV-1 outlet is connected to the SOV-2 exhaust, and the actuator receives the final output from the SOV-2.
- Solenoid Valve-1 SOV-1 Failure
If SOV-1 fails, the SOV-1 output port is linked to the exhaust, and the air is leaving SOV-2 since SOV-2 is powered and the inlet is connected to the output.
Air Flow indicators are depicted with arrows in the illustration above.
- Solenoid Valve-2 SOV-2 Failure
If SOV-2 becomes failure then the SOV-2 outlet is connected to the exhaust and SOV-1 is energized then the air goes from the SOV-1 inlet to the outlet then the outlet is connected to the SOV-2 exhaust which is connected with the SOV-2 outlet in fail condition and the air is going to actuator.
Air Flow indications are shown in the above figure with the arrows.
- Solenoid Valve-2 SOV-1 and SOV-2 Both Failure
If SOV-2 fails, then the SOV-2 outlet is connected to the exhaust and SOV-1 is powered. The air then flows from the inlet port of SOV-1 to the outlet, which is connected to the SOV-2 outlet in the fail state.
Air Flow indicators are depicted with arrows in the illustration above.
How to Evaluate the SOV Quality and Stability of an Operating Plant
Utilize a pyrometer to determine the SOV’s monthly surface temperature. The surface temperature is nearly comparable if both SOVs are manufactured by the same company. (Maximum difference between both SOV is 5 degrees Celsius.) Check the coil resistance if the temperature differential is greater.
Physically inspect the exhaust port to make sure it is not jammed and is operating normally.
Control Valves 101: Valve Types, Applications, Components, and Accessories
Case Study: Control Valve With the Interlock Shut-off Function
Question: Does this control valve with the interlock shut-off function in the picture have to be implemented with a solenoid valve in front of the positioner? Why can’t it be implemented in the DCS program? For example, set up a signal in the DCS to give the control valve a full open or full close when the interlock is triggered.
Answer: Control valve with interlocking shut-off function requirements, need to install a solenoid valve in the front of the positioner. The following 3 reasons are for your reference.
1. The positioner sometimes acts relatively slowly (the positioner output is usually a constant value, and the diaphragm actuator of the control valve varies in size), which does not meet the “fast response” requirement.
2. The positioner input signal – valve position relationship is often not very accurate, and when the deviation is not significant, it does not affect the operation of the system and is not detected (the actual maintenance often encountered when the positioner needs to be adjusted when during maintenance), so the control signal through the positioner to achieve the control valve shutdown is not necessarily reliable.
3. The reliability of the safety interlock requires that the interlocking action signal and the fault signal are consistent (the action signal of the interlocking signal is in the same form and the performance of the lost signal line), while the closing signal of the positioner is 4mA or 20mA, which cannot meet this requirement.
The above analysis is not necessarily comprehensive, but the interlocking system to achieve the required control room power failure or control room to the control valve signal wire failure (eg: bridge break) when the control valve can ensure shutdown, but also must have universal guidance (to form a specification), “control valve with interlock shutdown, must be between the control valve and the positioner install a solenoid valve to achieve” has become the principle to observe.
- HGT-20507 in the provisions of 11.9.3 solenoid valve selection should meet the following requirements: for remote control, process control, and interlocking systems, to achieve automatic closure of the air supply system, so that the control valve open or closed occasions.
- SHT3005 remote control, process control, and interlocking systems, to achieve automatic shutdown of the air supply system, control valve switching and other occasions, which should be selected for low power (less than 4W) three-way or four-way solenoid valve. The low-power solenoid valve may not be suitable for special control valves.
- The company’s corporate standards: If the control valve as the final component of the SIS interlock that has SIL level requirements, it needs to have solenoid valve action, while the corresponding controller with manual, given the corresponding output. In general, the control valve of DCS interlocking action without SIL level requirements does not require a solenoid valve, the action will correspond to the controller with manual, given the corresponding output.
Combined with the specifications and company requirements, against P&ID practices, the configuration of solenoid valves is recommended as follows.
1) Control valves participating in IPL (whether DCS or SIS) interlocking, should be equipped with solenoid valves.
(2) in the control valve on the pipeline without a shut-off valve, and the process that the operation interlocking requirements are relatively high (solenoid valve can be understood as a switch for the light, 4-20mA for the light knob), can be considered with solenoid valve.
Top 7 Control Valve Manufacturers In Europe
What Is Pneumatic Solenoid Valve
A pneumatic solenoid valve is a type of valve used to control the flow of air in a pneumatic system. It’s an electromechanical device that uses an electromagnetic solenoid to actuate the valve mechanism.
The solenoid in the valve consists of a coil of wire that creates a magnetic field when an electric current is passed through it. This magnetic field attracts a movable metal plunger or armature inside the coil, and this movement either opens or closes the valve.
How It Works:
When an electrical current is applied to the solenoid coil, it creates a magnetic field that attracts the plunger, causing it to move.
Depending on the design of the valve, this movement either opens or closes the valve, controlling the flow of air in the system.
When the electrical current is removed, the magnetic field disappears, and a spring returns the plunger to its original position, either opening or closing the valve.
Pneumatic solenoid valves can be normally open (NO), normally closed (NC), or be capable of switching between both states.
- Normally open (NO): In the de-energized state, the valve allows air to pass through. When energized, the valve closes and stops the flow of air.
- Normally closed (NC): In the de-energized state, the valve blocks the flow of air. When energized, the valve opens and allows air to pass through.
Pneumatic solenoid valves are often used in automation systems and various industrial applications where precise control over the flow of air is required.
What Is Level Control Valve Function
A level control valve is used to regulate the level of a fluid within a tank, reservoir, or other container. It works by either adding or removing fluid in response to changes in the fluid level to maintain it within a specified range.
Here’s how it generally functions:
- Sensing: A level control valve is often paired with a level sensor, which detects the current level of fluid in the container. The sensor may use various technologies to detect the level, such as float switches, ultrasonic sensors, or capacitive sensors.
- Control: Based on the signal from the level sensor, the control valve adjusts its position. If the level sensor detects that the fluid level is too high, it signals the control valve to close or partially close in order to reduce the inflow of fluid or allow fluid to be drained. If the fluid level is too low, the valve opens to allow more fluid in.
- Regulation: Through this continuous process of sensing and control, the level control valve can maintain the fluid level within a desired range, ensuring the smooth operation of the system and preventing issues like overflows or shortages.
Level control valves are used in a wide variety of applications, including water treatment plants, oil and gas storage facilities, chemical processing plants, and HVAC systems, among others. They play a crucial role in maintaining the correct operating conditions in these systems.