pvc ball valve leaking from handle
12 gate valve dimensions
axial check valve supplier
valworx 3 way valve
At its core, a pressure safety valve is a specialized device engineered to automatically release excess pressure from within a system when the pressure exceeds maximum allowable working pressure. These valves are viewed as pressure relief devices that are crucial in all industrial systems, designed to automatically responding to overpressure events and preventing the system from reaching dangerous levels that could lead to equipment damage, process disruptions, or, in extreme cases, catastrophic failures. A pressure safety valve, often referred to as a safety relief valve, PRV or PSV, is a crucial component that ensures the integrity and safety of industrial processes. Its significance lies in the pivotal task of maintaining safe operating conditions within a system, preventing catastrophic failures and safeguarding both personnel and equipment.
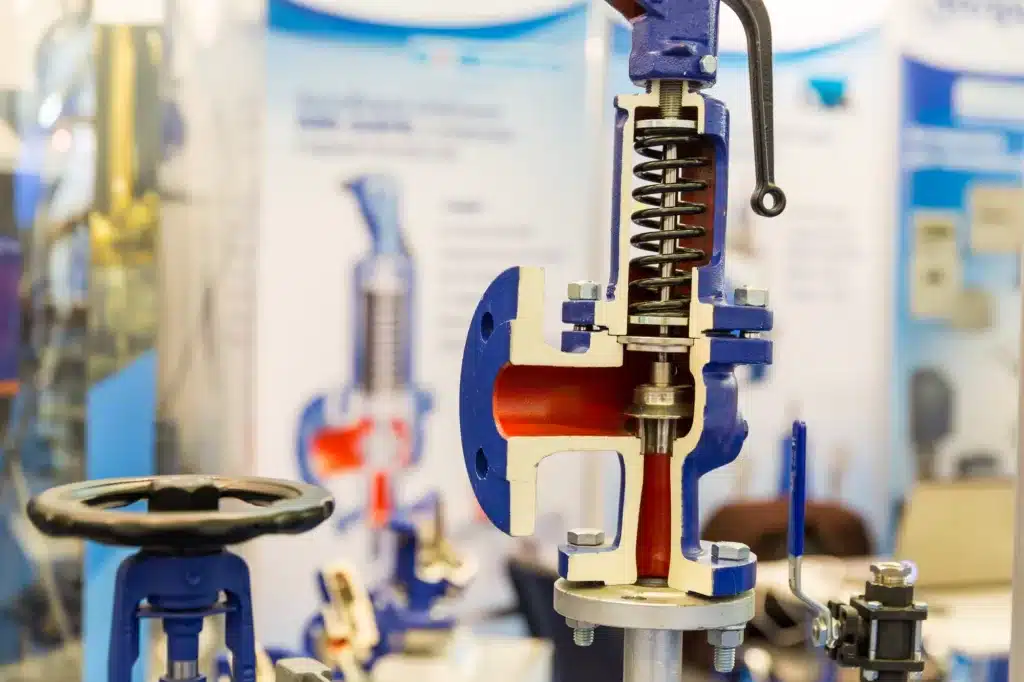
Basics of Pressure Safety Valves
A. Definition and Purpose
At its essence, a pressure safety valve (PSV) is a One of the most critical automatic safety devices designed to prevent overpressure scenarios within industrial systems. Its fundamental purpose is to safeguard equipment, processes, and personnel during an over-pressure event in a pressurized vessel or equipment by automatically relieving excess pressure when the system’s operational limits are exceeded. This fail-safe mechanism is indispensable in avoiding potential disasters that could arise from uncontrolled pressure build-up. A pressure safety valve is carefully engineered to automatically open and release surplus pressure from pressure vessels or equipment, ensuring a rapid return to normal conditions before securely re-closing to prevent any further fluid release.
B. Components and Mechanism of Action
1. Valve Disc, Seat, and Spring
The core components of a pressure safety valve include the valve disc, seat, and spring. The valve disc is a movable element that sits against the seat, forming a tight seal under normal operating conditions. The spring, calibrated to a specific tension, exerts force on the disc, counteracting the system pressure. When the pressure surpasses the inlet pressure, the spring tension is overcome, causing the valve disc to lift from the seat. This rapid action creates an opening for the excess pressure to escape, reinstating a balance within the system.
2. Set Pressure and Opening Mechanism
The set pressure, also known as the relief pressure or popping pressure, is the threshold at which the pressure safety valve activates. It is a predefined value based on the system’s operational requirements and safety considerations. The opening mechanism involves the interplay between the spring force and the opposing system pressure. When the system pressure exceeds the set pressure, the valve opens, allowing the discharge of pressurized fluid. This controlled release ensures that the system returns to a safe pressure range, preventing potential hazards.
Types of Pressure Safety Valves
A. Spring-Loaded Pressure Safety Valves
Spring-loaded pressure safety valves are the most common and straightforward type. Their design includes a spring that applies force to the valve disc to keep it closed. Once the system pressure surpasses the preset limit, the spring force is overcome, allowing the valve to open and discharge excess pressure.
B. Pilot-Operated Pressure Safety Valves
Pilot-operated pressure safety valves use a pilot valve in addition to the main valve. The pilot valve senses the system pressure and controls the opening and closing of the main valve. This design offers greater accuracy and is often used in applications with variable pressure conditions.
C. Other Varieties
Beyond the primary categories, various other specialized pressure safety valves exist to serve a specific industrial requirements. These may include balanced-bellows safety valves, diaphragm safety valves, or pressure relief valves with specific features designed for distinct operational scenarios. Exploring these diverse variants ensures optimal selection based on the unique needs of different applications.
Working Principles
A pressure safety valve (PSV), often referred to as a pressure relief valve (PRV), is a type of safety valve used to control or limit the pressure in a system; it is designed to open at a predetermined set pressure to protect equipment and systems from being subjected to pressures that exceed their design limits. Here’s how it typically works:
- Set Pressure: Each PSV is set to open at a specific pressure known as the “set pressure,” which is determined based on the maximum allowable operating pressure of the system it protects. The set pressure is usually a little higher than the system’s normal operating pressure but below the maximum pressure the system can handle.
- Spring-Loaded Mechanism: Many PSVs are spring-loaded. A spring inside the valve applies a force that keeps the valve closed under normal conditions. The force exerted by the spring is calibrated to balance against the system pressure.
- Pressure Exceeds Set Point: When the system pressure increases and exceeds the set pressure of the valve, the force exerted by the pressurized fluid overcomes the spring force. This imbalance causes the valve to open, allowing fluid (gas, steam, or liquid) to flow out of the system through the valve.
- Relief of Excess Pressure: By opening, the PSV relieves the excess pressure, discharging enough fluid to bring the system pressure back down to a safer level. The discharge is typically directed to a safe location where it will not pose a hazard.
- Automatic Reclosing: Once the pressure in the system falls below the set pressure, the spring force pushes the valve back to its closed position, preventing further release of fluid. This automatic reclosing function is crucial as it allows the PSV to respond to future overpressure events without manual intervention.
- Overpressure Protection: The primary function of a PSV is to prevent equipment damage, explosions, or failures due to overpressure. By limiting the system pressure, it ensures the safety and integrity of the equipment and the safety of personnel.
- Testing and Maintenance: Regular testing and maintenance of PSVs are crucial. They should be periodically inspected and tested to ensure they open at the correct set pressure and are in good working condition.
Applications and Industries
A. Diverse Applications in Various Sectors
Pressure safety valves find widespread applications across diverse sectors due to their critical role in maintaining safe operating conditions. From petrochemical plants and manufacturing facilities to energy production and water treatment, these valves are integral to preventing overpressure events and ensuring the reliability of industrial processes.
B. Key Industries That Rely on Pressure Safety Valves
- Chemical Industry: In chemical processing, pressure safety valves safeguard against potential hazards associated with the handling of unstable substances.
- Oil and Gas: Petrochemical refineries heavily rely on pressure safety valves to protect equipment from overpressure situations, ensuring continuous and safe operations.
- Power Generation: Power plants, whether thermal or nuclear, use pressure safety valves to maintain optimal pressure levels in steam systems, preventing damage to turbines and boilers.
- Water Treatment: Pressure safety valves play a crucial role in water treatment plants, preventing excessive pressure in pipelines and ensuring the integrity of the water distribution system.
Exploring these applications highlights the versatility and indispensable nature of pressure safety valves across various industries.
Selection and Installation
A. Factors to Consider When Choosing Pressure Safety Valves
Selecting the right pressure safety valve is a critical decision that involves several key considerations:
- System Parameters: Understanding the specific requirements of the system, including operating pressure, temperature, and flow rates, is crucial for selecting a valve that aligns with these parameters.
- Valve Type: Choosing between spring-loaded or pilot-operated valves based on the application and industry requirements ensures optimal performance.
- Material Compatibility: Considering the compatibility of valve materials with the processed fluids to prevent corrosion or degradation over time.
B. Proper Installation Practices
Ensuring the correct installation of pressure safety valves is essential for their effectiveness and longevity. Key practices include:
- Location and Orientation: Placing the valve in a position where it can effectively release excess pressure and ensuring the correct orientation for optimal performance.
- Piping and Venting Considerations: Properly sizing and designing the piping system connected to the valve to facilitate smooth pressure relief and venting. This involves accounting for potential backpressure and minimizing bends or restrictions in the piping.
Considering these factors and following proper installation practices is essential for the optimal performance of your pressure safety valve. For professional guidance and expert installation, trust THINKTANK, a company committed to ensuring the highest standards in safety valve installation for industrial systems.
Maintenance and Inspection
A. Regular Checks for Optimal Performance
Effective maintenance and regular checks are vital to ensure the pressure safety valve functions optimally over time. The following practices contribute to its longevity:
- Periodic Schedule: Establishing a routine maintenance schedule based on industry standards and the valve manufacturer’s recommendations.
- Visual Inspection: Regularly examining the valve for visible signs of wear, corrosion, or damage that could compromise its performance.
- Functional Testing: Conducting periodic tests to confirm the valve’s response and proper operation under simulated pressure relief conditions.
- Calibration Verification: Ensuring the valve’s calibration aligns with the specified set pressure, providing accurate and reliable relief.
B. Identifying Signs of Wear and Issues
Routine inspections should include a detailed assessment for potential wear and issues, focusing on the following indicators:
- Leaks: Detecting any fluid or gas leakage around the valve, which may signify a compromised seal.
- Corrosion: Checking for signs of corrosion on the valve body or components, addressing potential material degradation.
- Unusual Sounds: Listening for abnormal sounds during valve operation, as they could indicate mechanical issues.
- Irregular Pressure Relief: Monitoring for instances where the valve activates inconsistently or fails to relieve pressure, suggesting a malfunction.
By incorporating these maintenance practices and attentively identifying signs of wear, operators can ensure the pressure safety valve remains reliable and ready to safeguard against overpressure events.
Summary
In summary, a pressure safety valve plays a crucial role in maintaining the safety of pressurized systems, automatically relieving excess pressure to prevent potential hazards. Ensuring the optimal performance of these valves is essential for industrial operators, and we, THINKTANK, offer comprehensive services, from professional installations to ongoing maintenance, to guarantee the reliable and efficient operation of safety valves. For further insights into safety valves and safety relief valves, explore our blogs.