butterfly check valve
electric butterfly valve
manual butterfly valve
butterfly valve 4 inch
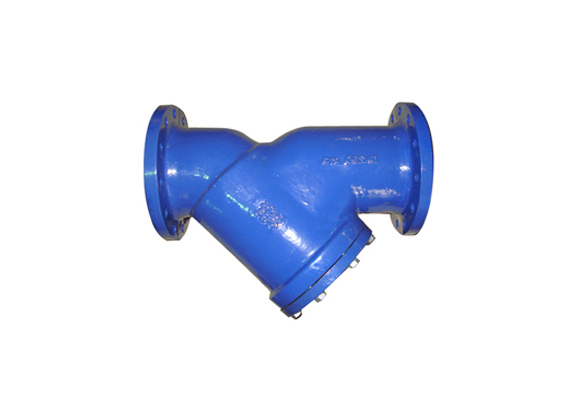
6″ butterfly valve
Both ball valves and solenoid valves serve a wide variety of applications. From a 3 way ball valve to a gas solenoid valve, one can find them employed anywhere from the domestic to the industrial sectors. When contemplating the decision between these two categories of valves, many considerations should factor into the evaluation including actuation arrangement, power supply, size, pressure, speed, materials of construction, and failure mode to name a few.
Actuation Arrangement
One should consider how one intends to drive the valve under consideration. A ball valve has a variety of options in regard to possible actuation. The valve itself proves independent of the device with which it can interface in order to stroke the valve. One can install a pneumatic actuator to drive the action of the valve based on pressurized air, an electric actuator to motorize the operation of the valve by an electric signal or simply install a lever or handle so that the function of the valve remains a product of manual operation.
This does not prove the case with a solenoid valve whose actuation involves sending an electric current to magnetize a ferromagnetic coil intrinsic to the construction of the valve in order to stroke the device open or closed. Thus, it can only operate by means of an electric signal to power the valve.
Power choices
Though a ball valve can utilize an electric actuator, most frequently offering either 120 VAC or 24 VDC power supplies, a solenoid valve typically can provide a more robust array of choices as far as AC or DC options in this regard. But the nature of the actuation remaining non-intrinsic to the valve itself also allows such ball valve assemblies to provide more manual override options. When present, a manual override allows one to stroke a valve open or closed by some method of manual operation, often a handwheel, that overrides the actuator.
Size
The required valve size plays a significant role in deciding between a ball valve versus a solenoid. In terms of the space envelope required for installation, solenoids offer a more compact package than that of actuated ball valves. But if this window does not prove of specific concern, on smaller sizes of 2” or less, both choices may prove suitable selections. But solenoids prove limited in this respect. Smaller solenoid valves can operate in a direct acting fashion where the action of the solenoid directly opens or closes the flow path. However, as the required valve size grows to accommodate a larger flow, manufacturers adapt the solenoid’s functionality to a pilot-operated configuration. In this arrangement, the solenoid’s action opens or closes a pilot valve that in turn influences the opening or closing of the main flow path. This pilot assisted operation requires a pressure differential in order to operate, which does not necessarily prove the case with a ball valve. Ball valves do not have this sizing limitation nor specific reliance on piloted operation in larger sizes. Availability in larger sizes necessarily means that ball valves have the capacity of accommodating higher flows than that of a solenoid overall. But even on comparable line sizes, the Cv factors for ball valves remain likely to eclipse those of solenoids.
Operating pressure
The pressures involved in one’s application also serve as a determining factor as to whether to employ a solenoid or a ball valve. While different designs of either option accommodate different working pressures, a high pressure ball valve might accommodate a working pressure in the hundreds, thousands, or even tens of thousands of psi. A solenoid likely remains limited to accommodating somewhere in the hundreds of psi. This limitation of working pressure influences both the maximum inlet pressure and back pressure on the discharge side of the valve that such a device can face and still operate. Thus, in an application facing elevating operating pressure or intermittent pressure spikes, a high pressure ball valve remains a more suitable selection.
Speed and Cycle Life
Depending upon the particulars of the application, operating speed may represent a preeminent concern in terms of valve selection. Solenoid valves tend to have the fastest response time in this regard enabling them to cycle more quickly than a ball valve within the same interval. Electrically actuated ball valves, in particular, can prove slow to stroke both while opening and closing, measuring that period in seconds as opposed to the sometimes milliseconds of the solenoid. Further, the electric actuator of the ball valve may very well have a limited duty cycle meaning that it requires a specific ratio of non-operating time versus active operating time in order to avoid overheating the motor. In addition to cycling more quickly, a solenoid valve also tends to have a significantly higher cycle life as well. This means that, under ideal operating conditions, the number of opening/closing cycles performed by the device before requiring maintenance or replacement will prove orders of magnitude greater in a solenoid.
Materials of Construction
While manufacturers mostly offer solenoids in stainless steel and brass options, the construction of ball valves prove much more diverse. In addition to the more typical metallic offerings of bronze, carbon steel, and stainless steel, one also finds offerings in plastics like PVC, PVDF, and Polypropylene, or even exotic alloys like Hastelloy and Alloy 20, significantly eclipsing the typical offerings available for a liquid or gas solenoid valve. The array of construction materials enables ball valve offerings to address more diverse requirements of chemical compatibility. While both ball valves and solenoids can function well on clean gas and liquid applications, the design and material selection of a ball valve can make it more effective in its resistance to contaminants and particulates that infiltrate the subject media. Ball valves also offer more diversity in end connection options than do most solenoids. While one can find both valve offerings with either threaded or flanged connections, some ball valves boast tri clamp connections making them suitable for installation in sanitary applications or even socket-weld connections enabling one to employ them where welding in place proves necessary. The materials of construction and ability to have welded ends represent just some of the factors that make these quarter-turn devices better suited to applications involving more extreme temperatures.
Failure Mode
One of the significant benefits of a 2 way or even a 3 way solenoid valve remains its intrinsic fail-safe design that includes a predictable fail-position as a standard feature as opposed to a costly adder as would prove the case on a ball valve assembly. A two-way solenoid offers either a normally closed or a normally open configuration. When de-energized the valve will return to its normal position via a spring. Even in a 3 way solenoid valve, the device has only two states, energized and de-energized regardless of the porting. Here too the valve returns to its normal state via a spring when de-energized. In a double acting, pneumatically actuated ball valve or a typical electrically actuated ball valve, the valve will fail in place on loss of its actuation signal and not automatically return to a designated position. This would apply to a 2 way version, a 3 way ball valve, or any multi-ported arrangement. While spring return pneumatic actuators and fail-safe electric actuators that include springs or battery packs address this necessity, they often prove heavier, larger, and certainly more costly than the non-fail-safe versions. The nature of this distinction often makes solenoid valves a less costly option in many fail-safe applications.
On-off versus modulating control
When speaking of controlling the operation of a valve in respect to its role in the process, one must determine whether the valve in question only needs to operate in the two states of open or closed, or does the application require that it potentially modulate through several different stages between open and closed in order to serve its purpose. This represents the difference between modulating and on-off valves. Given the duality of its energized versus de-energized states, the solenoid serves the function of on-off control quite well in a highly responsive and highly reliable fashion. But when it comes to selecting a valve for modulating service, ball valve assemblies prove more adaptable in this regard through the inclusion of a modulating card in an electrically actuated assembly or a pneumatic or electropneumatic positioner installed on an air driven assembly. Further, manufacturers can machine a v-slot into the ball itself in order to fine tune the control of media through the valve as its actuator modulates.
Having difficulty determining whether an application requires a ball valve versus a solenoid valve? The experts at ValveMan have the knowledge and experience to help. Shop ValveMan.com today!
Related Products
[[7125]]