non-slam check valves
spirax pressure reducing valve
s2000 idle air control valve
axial check valve manufacturer
As the director of THINKTANK, a leading provider of industrial valve solutions, Today I received an insightful question from one of our valued customers regarding the closing time of pinch valves and knife gate valves with hydraulic actuators. This question highlights a common concern among industry professionals about the efficiency and performance of valve systems in various applications. Today, I want to address this query in depth, aiming to shed light on the factors affecting the closing time of hydraulic actuator valves and how to optimize your valve selection for the best performance. Noted: If there are any errors during the article, please kindly to contact me to correctly it.
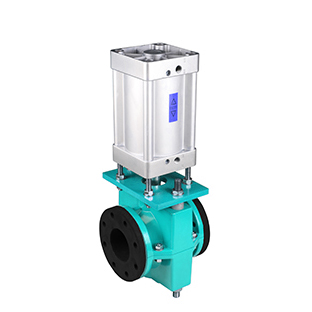
The Importance of Valve Closing Time
Valve closing time is a critical parameter in many industrial applications, impacting everything from the safety and reliability of the system to its efficiency and operational costs. Understanding and optimizing the closing time can prevent issues such as water hammer, ensure precise flow control, and enhance system responsiveness.
A Brief Overview of Hydraulic Actuators
Hydraulic actuators are favored in many industrial settings for their robust performance, providing high force output and precise control over valve positioning. They operate by using hydraulic fluid to move a piston, which in turn moves the valve to the desired position.
Factors Influencing Closing Time
The following are the important 4 factors which can influencing industrial valve closing time.
1. Hydraulic Fluid Pressure
The pressure of the hydraulic fluid significantly influences the actuator’s force and, consequently, the speed at which the valve closes. Higher pressures can achieve faster closing times.
2. Actuator Size and Type
The physical size of the actuator and its design (single or double-acting) affect the volume of hydraulic fluid needed to move the actuator piston, which in turn impacts the speed of operation.
3. Valve Size and Design
Larger valves require more force to close, which might slightly increase the closing time due to the larger surface area resisting movement.
4. Hydraulic System Design
The efficiency of the hydraulic system, including the diameter of hydraulic lines, the type of hydraulic fluid, and the presence of any flow restrictors, can affect the speed at which hydraulic fluid is delivered to the actuator.
Pinch Valve Closing Time
The closing time of a pinch valve is influenced by the following factors:
a. Air Pressure
The higher the control air pressure, the faster the sleeve (or tube) of the pinch valve will close. However, there’s a limit to how fast the sleeve can compress without damaging the valve or the sleeve itself.
b. Sleeve Material and Thickness
The material and thickness of the sleeve affect its flexibility and how quickly it can deform to stop the flow.
c. Valve Size
Larger valves may take longer to close due to the larger volume of the sleeve that needs to be compressed.
d. Control System
The design of the pneumatic control system, including the speed of air exhaust, also impacts the closing time.
Knife Gate Valve Closing Time
The closing time of a knife gate valve is influenced by these factors:
a. Actuator Type
Knife gate valves can be operated manually, pneumatically, electrically, or hydraulically. Pneumatic and hydraulic actuators typically offer faster operation than manual or electric actuators.
b. Gate Size and Weight
Larger and heavier gates take more time to move, especially if the actuator power is not proportionately increased.
c. Valve Design
Some knife gate valves are designed for quick operation, featuring optimized flow paths for rapid actuator response.
d. System Pressure and Friction
The pressure in the system and the friction within the valve mechanism can affect how quickly the gate can be moved to the closed position.
Estimating Closing Times
Given the above factors, you can estimate the closing time with a more specific focus on the hydraulic system’s capabilities. The formula remains similar:
Where
- Distance to Close refers to the travel distance from the fully open to the fully closed position.
- Speed of Actuation depends on the actuator type and operating conditions.
However, for hydraulic systems, the Speed of Actuation can be estimated based on the hydraulic fluid flow rate and the effective area of the actuator piston:
Where:
- Flow Rate is the rate at which hydraulic fluid is delivered to the actuator, typically in liters per minute (L/min).
- Effective Area of Piston is the cross-sectional area of the piston in the hydraulic actuator, typically in square centimeters (cm²).
In practice, it’s essential to refer to the manufacturer’s specifications for both pinch and knife gate valves to get accurate closing times. If you’re considering specific valve models and have their parameters, I can help you with a more detailed calculation or estimation.
Optimizing Valve Selection
Selecting the right valve and actuator combination for your specific application involves understanding the demands of your system and the characteristics of different valves and actuators. Here are detailed strategies and considerations to ensure optimal performance and reliability:
1. Define Your System Requirements
Start by clearly defining the operational parameters and requirements of your system. Consider aspects such as:
- Flow Rate: The maximum and minimum flow rates your system needs to handle.
- Pressure: The operating pressure range within your system.
- Fluid Type: The type of fluid (gas, liquid, corrosive nature, etc.) the valve will be controlling.
- Temperature: The temperature range within which the system will operate.
- Environmental Conditions: External conditions that may affect the valve’s operation, such as outdoor placement or exposure to corrosive environments.
2. Understand Valve and Actuator Types
Different valve and actuator types offer distinct advantages and limitations. For instance:
- Pinch Valves are excellent for handling slurry or highly viscous fluids but may not be suitable for high-pressure applications.
- Knife Gate Valves offer a robust solution for systems requiring a valve that can cut through thick materials or operate under higher pressure.
- Hydraulic Actuators provide high force and precise control, making them ideal for heavy-duty applications, but require a reliable source of hydraulic power.
3. Consult with Manufacturers
Manufacturers have a wealth of knowledge and data on the performance of their products. Discuss your application’s specifics with them to get recommendations on the most appropriate valve and actuator types. They can provide insights into:
- Valve Material Compatibility: Ensuring the valve materials are compatible with the fluids in your system to prevent corrosion or degradation.
- Actuator Force and Speed: Matching the actuator’s capabilities to the valve’s requirements, ensuring it can operate the valve efficiently under all conditions.
4. Prioritize Quality and Reliability
Investing in high-quality valves and actuators from reputable manufacturers can significantly reduce maintenance costs and downtime over the system’s life. Look for products with:
- Proven Track Records: Opt for brands and models known for their durability and reliability.
- Warranty and Support: Consider the level of after-sales support and warranty coverage, which can be indicative of the manufacturer’s confidence in their product.
5. Tailor to Application-Specific Needs
Every application has unique requirements, and selecting a valve and actuator should reflect this:
- Rapid Response: For systems requiring quick shut-off to prevent surges or other issues, consider valves and actuators with fast response times.
- High Precision: Applications requiring precise flow control may benefit from actuators with variable control options and valves designed for fine adjustments.
- Heavy-Duty Operation: For systems with high pressure or demanding conditions, choose valves and actuators designed for such environments to ensure longevity and reliability.
6. Simulate and Test
Where possible, simulate the operating conditions to test how the valve and actuator perform together. Simulation can help identify any potential issues before they become problematic in actual operations. Consider factors like:
- Flow Characteristics: How the valve responds to changes in flow rate or pressure.
- Actuator Behavior: How quickly and accurately the actuator responds to control signals under different conditions.
Conclusion
Understanding the closing time of valves with hydraulic actuators is essential for optimizing the performance and reliability of industrial systems. By considering the factors outlined above and working closely with experienced manufacturers, you can ensure that your valve selection meets the specific needs of your application.
At THINKTANK, we’re committed to providing our clients with the knowledge and solutions needed to make informed decisions about their valve and actuator needs. If you have further questions or require assistance in selecting the right valve solution, our team of experts is here to help.