“12”” gate valve”
mueller gate valve diagram
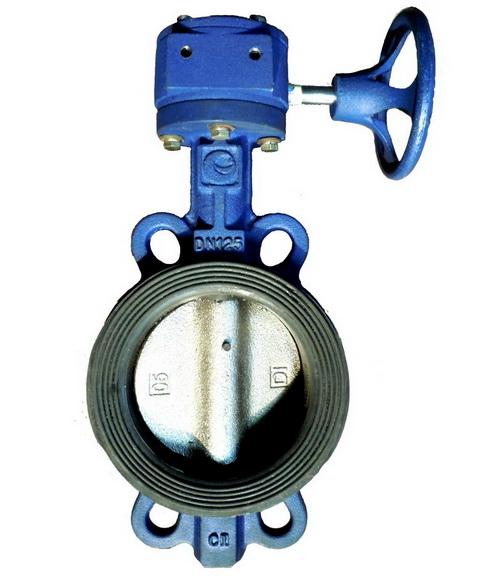
March 18, 2024 by Brina
If you’re looking for everything about swing check valves, this is the right article for you.
Read on to discover the nitty-gritty below:
Table of Contents
Toggle
- What Are Swing Type Check Valve?
- Swing Check Valve Diagram
- Types of Swing Check Valves
- 1. Standard Swing Check Valve
- 2. Lift Check Valve
- 3. Tilting Disc Check Valve
- 4. In-line Check Valve
- 5. Dual Plate Check Valve
- 6. Wafer Check Valve
- 7. Silent Check Valve
- 8. Nozzle Check Valve
- 9. Spring-Assisted Check Valve
- Swing Check Valve Installation Position Types
- 1. Horizontal check valve installation
- 2. Vertical check valve installation
- 3. Inclined or sloped installation
- 4. Flap type installation
- 5. Multi-angle installation
- 6. Downward flow installation
- 7. Upward flow installation
- 8. Side entry installation
- Benefits of Swing Check Valves
- 1. Backflow Prevention
- 2. Simple and Reliable Design
- 3. Low-Pressure Drop
- 4. Quick Closure
- 5. Versatility in Installation
- 6. Low Maintenance Requirements
- 7. Suitable for Various Fluids
- 8. Reduced Noise
- 9. Bi-Directional Flow Capability
- 10. Space-Efficient Design
- Applications of Swing Check Valves
- 1. Water and Wastewater Treatment
- 2. Oil and Gas Industry
- 3. Chemical Processing
- 4. Power Generation
- 5. HVAC Systems
- 6. Marine and Shipbuilding
- 7. Mining Operations
- 8. Fire Protection Systems
- 9. Pulp and Paper Industry
- 10. Food and Beverage Processing
- Conclusion
What Are Swing Type Check Valve?
Swing check valves come in various types to cater to different applications and preferences.
The choice of a specific type depends on factors such as flow requirements, space limitations, noise considerations, and the need for additional features like quick closure or water hammer prevention.
Understanding the characteristics of each type helps in selecting the most suitable swing check valve for a given application.
Swing Check Valve Diagram
This diagram typically illustrates the internal components and working mechanism of a swing check valve.
Here’s a simple explanation of the key elements you might find in a swing check valve diagram:
Valve Body: The outer casing of the valve that contains and supports the internal components.
Inlet and Outlet Ports: Designated areas where fluid enters (inlet) and exits (outlet) the valve.
Swinging Disc: A disc, usually circular or semi-circular, positioned inside the valve that swings or pivots on a hinge. The swinging disc allows or blocks the flow of fluid.
Hinge or Pivot Point: The point at which the swinging disc is attached to the valve body, enabling it to move freely.
Seat: The sealing surface against which the swinging disc comes into contact when the valve is closed, preventing backflow.
Flow Arrow: Indicates the direction of fluid flow through the valve, helping with proper installation orientation.
Hinge Pin: The pin that serves as the axis of rotation for the swinging disc.
Check Valve Symbol: A symbol often included in diagrams to represent the swing check valve.
Optional Features: Additional features such as springs (in spring-assisted models) or counterweights that may be present for specific applications.
Types of Swing Check Valves
1. Standard Swing Check Valve
The most common type of swing check valve. Consists of a swinging disc that freely moves on a hinge to allow flow in one direction and prevent backflow when the flow stops.
2. Lift Check Valve
Similar to the standard type but has a disc lifted from the seat to open, providing a slightly better seal and reduced pressure drop.
3. Tilting Disc Check Valve
Instead of swinging, the disc tilts to open, allowing for a faster response to flow changes and reduced potential for the water hammer.
4. In-line Check Valve
Designed for installation directly in a pipeline, these valves allow for efficient flow control in a compact space.
5. Dual Plate Check Valve
Features two plates that swing on a hinge, providing quick closure and reducing the chances of water hammering.
6. Wafer Check Valve
Thin and lightweight design suitable for limited space; installed between flanges without the need for additional gaskets.
7. Silent Check Valve
Designed to minimize noise and water hammer effects during operation, making them ideal for applications where noise reduction is critical.
8. Nozzle Check Valve
Utilizes a nozzle and cone mechanism for flow control, offering a reliable seal and efficient prevention of backflow.
9. Spring-Assisted Check Valve
Equipped with a spring that assists in closing the disc quickly, reducing the chances of water hammer and improving overall performance.
Swing Check Valve Installation Position Types
The swing check valve installation position type depends on factors such as system configuration, flow requirements, and space constraints. Proper consideration of the installation position ensures effective operation and optimal performance of swing check valves in fluid handling systems.
1. Horizontal check valve installation
The valve is mounted horizontally in the pipeline. The swinging disc moves vertically to allow fluid to flow upward and prevent backflow.
2. Vertical check valve installation
The vertical swing check valve is installed vertically in the pipeline. The swinging disc moves horizontally to allow fluid to flow upward and prevent backflow.
3. Inclined or sloped installation
The valve is installed at an angle, neither purely horizontal nor vertical, offering flexibility in adapting to specific system configurations.
4. Flap type installation
This valve has a flexible flap instead of a swinging disc and can be installed in various positions, including horizontal, vertical, or inclined.
5. Multi-angle installation
This valve is designed to be versatile, allowing installation at different angles, and providing adaptability to specific flow and space requirements.
6. Downward flow installation
The valve is Installed to allow downward fluid flow. The swinging disc moves to permit flow in the downward direction while preventing backflow.
7. Upward flow installation
The valve is installed to allow upward fluid flow. The swinging disc moves to permit flow in the upward direction while preventing backflow.
8. Side entry installation
The valve is installed with entry from the side, which allows for installation flexibility based on the piping system layout.
Benefits of Swing Check Valves
Swing check valves offer multiple benefits, including effective backflow prevention, making them a popular choice in fluid handling systems across different industries.
Here are a few more benefits that swing check valves offer:
1. Backflow Prevention
Swing check valves effectively prevent backflow by allowing fluid to flow in one direction and automatically closing to stop reverse flow.
2. Simple and Reliable Design
The design is straightforward, with a swinging disc that opens and closes based on the direction of fluid flow, providing reliability in operation.
3. Low-Pressure Drop
When open, swing check valves offer minimal resistance to flow, resulting in low-pressure drop across the valve.
4. Quick Closure
The swinging disc quickly closes when the flow stops, minimizing the risk of water hammer and pressure surges in the pipeline.
5. Versatility in Installation
Swing check valves can be installed horizontally, vertically, or at different angles, providing flexibility in adapting to various piping system configurations.
6. Low Maintenance Requirements
The simple design and few moving parts contribute to low maintenance needs, making swing check valves cost-effective over time.
7. Suitable for Various Fluids
Swing check valves are versatile and suitable for a wide range of fluids, including liquids and gases, making them applicable in diverse industries.
8. Reduced Noise
Properly functioning swing check valves contribute to reduced noise levels in the pipeline by preventing sudden closure and water hammer effects.
9. Bi-Directional Flow Capability
Swing check valves can handle fluid flow in both directions, providing flexibility in applications where the direction of flow may change.
10. Space-Efficient Design
Swing check valves typically have a compact design, making them space-efficient and suitable for installations with limited space.
Applications of Swing Check Valves
Swing check valves have many applications across various industries, including water and wastewater treatment, oil and gas, and chemical processing.
Their versatility in controlling fluid flow and preventing backflow makes them essential components in diverse industrial processes.
1. Water and Wastewater Treatment
Swing check valves are used in water and wastewater treatment plants to control the flow of water and prevent backflow in various stages of the treatment process.
2. Oil and Gas Industry
In the oil and gas industry, swing check valves are employed to regulate the flow of fluids in pipelines, preventing reverse flow and ensuring efficient operation.
3. Chemical Processing
Swing check valves play a vital role in chemical processing plants, where they help control the flow of chemicals and prevent the mixing of different substances.
4. Power Generation
Power plants use swing check valves in piping systems to control the flow of water, steam, or other fluids, ensuring the proper functioning of turbines and generators.
5. HVAC Systems
Heating, Ventilation, and Air Conditioning (HVAC) systems utilize swing check valves to regulate the flow of fluids, maintaining the desired temperature and preventing unwanted backflow.
6. Marine and Shipbuilding
In marine and shipbuilding applications, swing check valves are used in piping systems to control the flow of water, fuel, and other fluids on ships and offshore structures.
7. Mining Operations
Swing check valves find application in mining operations to control the flow of water, slurry, or other fluids in mining processes and drainage systems.
8. Fire Protection Systems
Swing check valves are integral to fire protection systems, where they help regulate the flow of water and prevent backflow to ensure the reliability of firefighting equipment.
9. Pulp and Paper Industry
In the pulp and paper industry, swing check valves are used in processes involving the transport of fluids such as water, chemicals, and pulpy materials.
10. Food and Beverage Processing
Swing check valves play a crucial role in the food and beverage industry, controlling the flow of liquids and preventing contamination in processing and packaging operations.
Conclusion
If you’re looking for a swing check valve manufacturer, Xintai has visible proof of exceptional quality and continual advancement.
Established in 1998, Xintai is a dynamic and trustworthy valve manufacturer based in China, showcasing a remarkable annual production of over 270,000 industrial valve units.
What sets Xintai apart is its dedicated team of experts and meticulous quality control specialists.
Their collective efforts ensure the production of high-quality valve products that have earned the trust of businesses worldwide, both on a global and international scale.
Contact them today via their website.